Manufacturers Unlock the Advantages of Laser Brazing
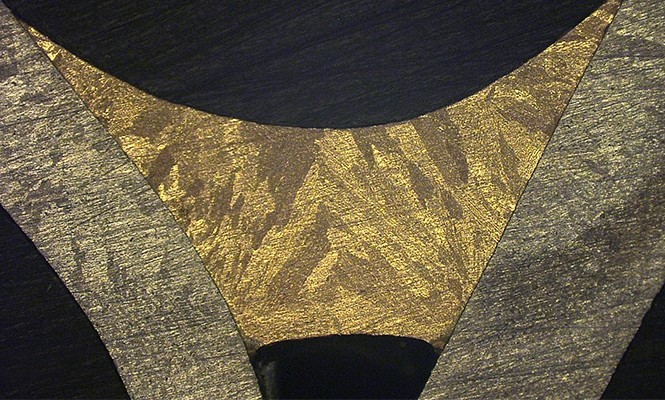
The advantages of laser brazing continue to expand as manufacturers discover new ways to optimize their production processes. Unlike conventional joining methods, laser brazing achieves superior results while offering enhanced flexibility and efficiency. By minimizing material usage and reducing the number of manufacturing steps, laser brazing helps companies cut costs without sacrificing quality.
If you're searching for a more efficient and cost-effective approach to metal joining, laser brazing could be the perfect solution for your business. Here's why this cutting-edge technology is gaining traction across multiple industries.
Understanding the Benefits of Brazing Over Traditional Methods
Brazing stands out as a highly effective technique for joining metal components. Unlike welding, which involves melting the base materials themselves, brazing uses a filler material that melts and flows into the joint to form a strong bond. This difference allows brazing to join dissimilar metals, offering greater versatility than welding alone.
Another significant advantage of brazing is its lower operating temperature compared to welding. This reduces the risk of thermal distortion in the base metals, preserving their structural integrity. Additionally, the reduced need for additional materials and simplified processes translates into cost savings and improved productivity.
Common brazing methods include torch brazing, arc brazing, furnace brazing, and induction brazing. Each approach has its own set of applications and benefits. For instance, torch brazing relies on a gas flame to heat the filler material, while arc brazing employs an electric current for the same purpose. Furnace brazing heats the entire assembly uniformly, making it suitable for complex geometries. Induction brazing, on the other hand, uses electromagnetic induction to generate heat precisely where needed.
How Laser Brazing Elevates the Industry Standard
Fiber laser brazing represents the next evolution in joining technology. By leveraging advanced laser systems, manufacturers achieve unparalleled precision and control over the brazing process. The laser efficiently melts the filler material while minimizing heat exposure to the surrounding base metals, ensuring minimal distortion and maximum joint strength.
One standout feature of laser brazing is its ability to operate without flux, eliminating the need for additional chemicals and further reducing costs. This clean, precise process enhances throughput and enables faster cycle times, making it ideal for high-volume production environments.
The fiber lasers used in these systems are typically solid-state designs requiring little maintenance. Their robust construction ensures consistent performance even in demanding industrial settings. Redundancy options like hot-swappable components further enhance reliability, guaranteeing uninterrupted operation regardless of external conditions.
Automation plays a crucial role in maximizing the potential of laser brazing. Robotic arms and sophisticated software work together to guide the laser beam accurately and consistently. As a result, each joint produced is virtually identical, eliminating variability caused by human error. This level of standardization not only improves product quality but also simplifies quality assurance procedures.
Genesis Systems provides comprehensive laser brazing solutions tailored to meet the unique demands of various sectors, including aerospace, aviation, and automotive manufacturing. Whether you're looking to enhance existing operations or implement new capabilities, our experts can help design a system that aligns with your specific requirements.
In conclusion, laser brazing offers numerous advantages over traditional methods, from improved accuracy and efficiency to reduced expenses and enhanced flexibility. If you're ready to take your manufacturing capabilities to the next level, consider exploring how laser brazing can benefit your organization today.
Posted in Laser Welding, Robotic Applications, Robotic WeldingServo Energy-saving Injection Molding Machine
Our machines include high-efficiency servo-energy saving injection molding machine, special injection molding machine, high-precision All-electric Injection Molding Machine and hybrid high-speed injection molding machine. They are suitable for auto parts industry, beverage packaging, electronic address book, home appliances industry, daily supplies, pharmaceutical industry, toys and gifts industry and construction industry, and a wide range of industries can choose according to their needs.
Servo Energy-Saving Injection Molding Machine,injection molding machine details,bottle preform making machine
Ningbo Haijing Plastic Machine Manufacturing Co. LTD , https://www.chinahaijing.com