Why Preventative Maintenance Is Essential for Automated Robotics
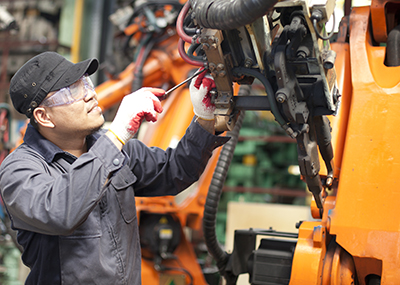
When a critical robotic system fails, the impact is immediate and often devastating. Whether you're a plant manager, robot technician, or business owner, you know all too well the chaos that follows an unexpected breakdown. Production lines grind to a halt, orders pile up, and your team is left waiting for repairs that could take days.
The Hidden Costs of Emergency Repairs
Many people underestimate the true cost of a robotic failure. It's not just about replacing a part or two—it’s about lost productivity, increased labor costs, and the stress of managing a crisis. When a machine goes down, your entire production line may be forced to stop, leading to idle workers and no output. This can result in missed deadlines, unhappy customers, and long-term damage to your company’s reputation.
Emergency parts procurement is usually done at a premium, with little time to negotiate or compare prices. Shipping costs also skyrocket when you need something delivered fast. Even after repairs are made, it can take weeks for your systems to return to full efficiency, making it nearly impossible to recover the lost time and revenue.
Preventative Maintenance Can Save You Money and Time
But there's a better way. A structured preventative maintenance program can significantly reduce the risk of unexpected failures. Regular inspections, cleaning, and component replacements help keep your robotic systems running smoothly and efficiently. While it may require some upfront investment, the long-term savings are well worth it.
Some businesses hesitate to implement a maintenance plan due to concerns about cost. However, consider the financial loss from even a single hour of downtime. By investing a little in routine care—like applying lubricants or checking connections—you can prevent costly emergencies and maintain consistent performance.
Why Outsourcing Makes Sense
Creating an in-house robotics maintenance team can be challenging. It requires training, resources, and ongoing management. For many companies, outsourcing this responsibility to a specialized provider is the smarter choice. A third-party service like Genesis Systems offers expert support, ensuring your equipment remains in top condition without the burden of internal management.
Our preventative maintenance services are designed to keep your automation systems running reliably. Visit our 24/7 Customer Service page to learn more about how we can help you avoid costly downtime and maximize efficiency.
Posted in Connected Solutions, Robot SafetyPrinted Tipping Paper,Printing Paper Staples,Cigarette Printing Paper,Tobacco Printing Paper
Jilin Changbaishan Packaging Materials Co., LTD , https://www.cbsbz.com