First, the experiment
(1) Experimental equipment
The pretreatment of dephosphorization with molten iron containing pre-melting dephosphorization agent containing converter slag is carried out in a molybdenum silicide resistance furnace with nitrogen protection (maximum temperature of 1600 ° C), as shown in Figure 1, the experimental temperature is selected at 1300 ~ 1400 ° C. A corundum crucible having a capacity of 100 mL was used as an experimental crucible, and a graphite crucible (having an inner diameter of 65 mm and a height of 120 mm) was used as a protective crucible, and was sampled and stirred with a Φ6 mm quartz tube.
(2) Experimental materials
The raw iron for the experiment is prepared by electrophilic pure iron, high-purity graphite powder and ferrophosphorus according to the listed target components, and is melted in a graphite crucible by an intermediate frequency induction furnace. The target molten iron composition is shown in Table 1 below.
1-nitrogen; 2-flow meter; 3-lightweight brick; 4- corundum crucible; 5--fused iron;
Table 1 Mass fraction of major chemical elements in pig iron %
w(C) | w(Si) | w(P) | w(S) | w(Mn) |
4.3 | 0.10 | 0.23 | 0.02 | 0.15 |
The dephosphorization agent uses Fe 2 O 3 and MnO in the iron oxide and converter slag (the composition of the converter slag as shown in Table 2) as the oxidant to analyze the pure CaO and the CaO and MgO in the converter slag as the fixing agent to analyze the pure CaF 2 is a fluxing agent. Each dephosphorization agent raw material is ground and sieved to a particle size of less than 0.15 mm, and then prepared according to a certain ratio.
Table 2 Quality fraction of each component of converter slag
w(CaO) | w(TFe) | w(Fe 2 O 3 ) | w(MgO) | w(SiO 2 ) | w(Al 2 O 3 ) | w(TiO 2 ) | w(MnO) | w(P 2 O 5 ) |
43.17 | 18.20 | 26 | 7.23 | 15.96 | 0.08 | 0.75 | 2.4 | 1.5 |
(3) Experimental methods
1. Preparation process of premelting dephosphorization agent containing converter slag
The raw materials are ground to a powder of 0.15 mm or less, and thoroughly mixed after being prepared according to a certain ratio. 100 g of 100 mg of corundum crucible is weighed, and then pre-melted in a molybdenum silicide resistance furnace to raise the temperature of the furnace. 1250 ~ 1300 ° C, after the furnace material is melted, stir it with a quartz tube, and keep it for 10 minutes for a short time (to prevent the Al 2 O 3 in the corundum crucible from entering the dephosphorization agent, affecting the dephosphorization effect of the pre-melting dephosphorization agent), immediately The crucible is taken out from the furnace, and the liquid residue is rapidly cooled, and the cooled pre-melting dephosphorization agent is pulverized to 0.15 mm or less for use.
2. Experimental process of dephosphorization by hot metal pretreatment with converter slag
The hot metal dephosphorization experiment was carried out in a siliconization furnace. During the experiment, a jacketed graphite crucible containing corundum of 300 g of raw iron was placed in a molybdenum silicide furnace for heating. When the temperature of the furnace was raised to 800 ° C, a nitrogen valve was opened to introduce nitrogen gas from the bottom of the furnace, and the flow rate of nitrogen was 5 L/min. After the temperature of the furnace rises to the predetermined temperature, the iron material is completely melted for 30 minutes, and the initial sample of molten iron is taken up with a Φ6mm quartz tube, and the dephosphorization agent is quickly added to the surface of the molten iron, and the reaction time is started to be recorded, and the dephosphorization reaction is started. The iron sample was taken up by a quartz tube for chemical analysis at 10 minutes, and the molten iron was stirred with a quartz rod every 3 minutes to improve the kinetic conditions of the iron-slag reaction.
Second, the experimental results and analysis
(1) Feasibility analysis of converter slag used for hot metal pretreatment
For hot metal pretreatment oxidative dephosphorization, it mainly oxidizes [P] in molten iron to P 2 O 5 by dissolving oxygen [O] in oxidizing agent Fe 2 O 3 added to dephosphorization agent, but P 2 O 5 is unstable and must react with the basic oxide CaO to form a phosphate slag (4CaO·P 2 O 5 or 3CaO·P 2 O 5 ) which can be stably present in the slag at a high temperature, so that the phosphorus in the molten iron is removed. The molecular theoretical reaction formula is as shown in the formula (1). At the same time, in order to adapt to the requirements of the hot metal pretreatment temperature (the hot metal pretreatment temperature is generally 1300 ~ 1400 ° C), reduce the melting point of the alkaline oxide, speed up the slag, increase the dephosphorization rate, and add a certain amount of help to the dephosphorization agent. Flux CaF 2 .
2[P]+5(FeO)+4(CaO)=(4CaO·P 2 O 5 )+5[Fe] (1)

For ordinary hot metal pretreatment dephosphorization agent w (Fe 2 O 3 ) is generally selected from 40% to 60%, w (CaO) is selected at 35% to 55%, and w (CaF 2 ) is between 5% and 15%. The converter slag is mainly composed of calcium oxide (38.4% to 48.5%), iron oxide (24.6% to 28.7%), and silicon oxide (8% to 15%). It can be seen that the composition and content of the converter slag and the hot metal pretreatment dephosphorization agent are similar. Therefore, the molten iron pretreatment dephosphorization can be realized by adding partial calcium oxide, iron oxide and fluorite to the converter slag. The pre-melting treatment is applied to the dephosphorization agent containing the converter slag, so that the chemical composition of the dephosphorization agent containing the converter slag is more uniform, the melting point and viscosity are low, the fluidity is good, the slag formation speed is fast, the effective treatment time is short, and the dephosphorization efficiency is high. It is easier to meet the requirements of hot metal pretreatment. At the same time, the converter slag resources are abundant, the price is cheap, and the processing is simple, which can effectively reduce the dephosphorization production cost and reduce environmental pollution. Therefore, converter slag is completely possible to replace some dephosphorization agents to achieve the purpose of hot metal pretreatment dephosphorization.
(II) Effect of converter slag ratio on dephosphorization of molten iron
Based on the optimal ratio of pre-melting dephosphorization agent determined by the purification reagent, 18.11%, 33.11%, 45.73%, and 56.49% of the converter slag portion were used instead of Fe 2 O 3 and CaO in the pre-melting dephosphorization agent. Preparation of dephosphorization agent. The pre-melting dephosphorization agent containing the converter slag was subjected to a dephosphorization experiment at 1350 ° C under the condition that the amount of molten iron was 10%. The results of dephosphorization treatment for 10 min are shown in Fig. 2. It can be seen that the partial demelting dephosphorization agent can be replaced by converter slag to achieve better dephosphorization effect. When the mass fraction of converter slag is 18.11% to 45.73%, the dephosphorization rate is obtained. It remained basically unchanged, all of which was greater than 91.43%, which reduced the phosphorus in molten iron from 0.21% to less than 0.018%, and the dephosphorization rate of 45.73% containing converter slag was slightly higher, which was 94.76%, and was prepared with purified reagents. The pre-melting dephosphorization agent has the same dephosphorization effect under the same conditions (the pre-melting dephosphorization agent prepared by the purification reagent can reduce the phosphorus in the molten iron to 0.0079%, the dephosphorization rate is 96.24%); when the dephosphorization agent is transferred When the mass fraction of slag is further increased to 56.49%, the dephosphorization rate is reduced to 73.33%, and the mass fraction of hot metal phosphate is reduced from 0.21% to 0.056%. This may be due to the fact that the dephosphorization component is constant. The increase of the amount of converter slag added, the P 2 O 5 content which is not favorable for the dephosphorization reaction is also increased correspondingly, so that the phosphorus-to-iron-to-iron distribution ratio (L p ) is lowered, and the dephosphorization effect is poor. Therefore, using about 45% converter slag instead of Fe 2 O 3 and CaO in the purification reagent to prepare the dephosphorization agent, the same dephosphorization rate as the pre-melting dephosphorization agent prepared by the purification reagent can be obtained, and a better desorption is achieved. Phosphorus effect.

(III) Effect of the amount of dephosphorization agent containing converter slag on dephosphorization effect
In order to study the effect of different pre-melting dephosphorization agents containing converter slag on the dephosphorization effect of hot metal pretreatment, at 1350 ° C, 45% of the pre-melting dephosphorization agent containing converter slag was added in the amount of molten iron. Dephosphorization experiments were carried out at %, 7%, and 10%. Figure 3 shows the dephosphorization rate change curve with different addition amounts when treated for 10 min. It can be seen that the dephosphorization rate increases with the increase of the addition amount. When the addition amount is 4%, the phosphorus in the molten iron is reduced from 0.21% to 0.095%. The phosphorus rate is only 54.76%. The reason for the poor dephosphorization effect is that the dephosphorization reaction is not fully carried out. The iron oxide and CaO in the dephosphorization agent do not fully oxidize and fix the phosphorus in the molten iron, so that the dephosphorization rate is lowered; When the amount is 7%, the dephosphorization rate is obviously improved, the phosphorus in the molten iron is reduced to 0.047%, the dephosphorization rate is 70.95%, and the dephosphorization rate is the highest when the addition amount is 10%, and the phosphorus in the molten iron can be The reduction was 0.011% and the dephosphorization rate was 94.76%. It was thus determined that the optimum addition amount under laboratory conditions was 10%. However, in actual industrial production, the amount of dephosphorization agent added should not be too much. Too much will not only increase production cost, increase the temperature drop of molten iron, but also cause oxidation loss of carbon and other elements in molten iron, and will increase the lining. The burden of erosion and subsequent processes loses its practical value. However, due to the small amount of molten iron in the laboratory (only about 300g at a time), the contact area of ​​slag- gold is relatively small, the kinetic conditions are poor, and the loss of the dephosphorization agent and the stirring rod, quartz sampling tube and crucible The slag of the wall makes the dephosphorization agent added insufficiently utilized, and in order to achieve a better dephosphorization effect, the amount of dephosphorization agent added is relatively high. However, in actual industrial production, it is only used as a theoretical guidance and practical reference. For the industrial production of dephosphorization agent, further industrialization experimental research is needed to determine.

(IV) Effect of treatment temperature on dephosphorization effect of converter slag dephosphorization agent
It is known from thermodynamic analysis that the dephosphorization reaction is a strong exothermic reaction (AH=-1033450 J/mol). The lower the temperature, the better the dephosphorization reaction proceeds in the positive direction, but the temperature is too low, the kinetic conditions of the dephosphorization reaction. Deterioration is not conducive to the dephosphorization reaction. To this end, the pre-melting dephosphorization agent containing 45% of the converter slag was subjected to the deionization test of molten iron at 1300, 1350 and 1400 ° C, respectively. The experimental results are shown in Fig. 4. When the treatment temperature is 1300 °C, the dephosphorization rate is only 19.05%, and when the experiment is carried out at this temperature, it is obvious that the dephosphorization slag becomes sticky, and the slag layer agglomeration and slag iron are not divided in a local area, which is due to the temperature. Too low, after adding the dephosphorization agent, the temperature drop of the molten iron is obviously increased, the kinetic conditions of the dephosphorization of the molten iron are deteriorated, the dephosphorization reaction cannot be sufficiently performed, and the dephosphorization rate is low. When the dephosphorization treatment is carried out at 1350 ° C and 1400 ° C, the dephosphorization rate is basically the same, both are about 95%, and the phosphorus in the molten iron can be reduced from 0.21% to about 0.010%. Therefore, it can be obtained that a pre-melting dephosphorization agent containing 45% of the converter slag can achieve a better dephosphorization effect when the dephosphorization pretreatment is performed at 1350 °C.

Third, the conclusion
(2) The dephosphorization effect of the pre-melting dephosphorization agent containing the transfer slag is equivalent to that of the conventional dephosphorization agent. When the conversion amount of the converter slag is about 45%, the dephosphorization effect of the pre-melting dephosphorization agent containing the transfer slag is most ideal. The mass fraction of hot metal phosphorus is reduced from 0.21% to 0.011%, and the dephosphorization rate is 94.76%.
(3) Temperature has a certain influence on the dephosphorization effect of hot metal pretreatment. The temperature is low and the kinetic conditions are deteriorated, which is not conducive to dephosphorization. The temperature is too high, which is not conducive to the improvement of thermodynamic conditions. After the experiment, the optimum temperature of the pre-melting dephosphorization agent containing the converter slag for hot metal pretreatment is 1350 °C.
(4) Under laboratory conditions, when the pre-melting dephosphorization agent containing converter slag is added in an amount of 10%, a better dephosphorization effect can be achieved.
All steel plates of good quality;Well sealed,no flying dust;Cold reduced blades,wear resistance;All high strength bolts in the joints;
It is mainly used to convey granula and powder materials,simple structured,easily operated,steady and reliable,which can charge and discharge at any place of the line;It is suitable for grain,feed,oil industries to horizontally convey granula and powder materials.
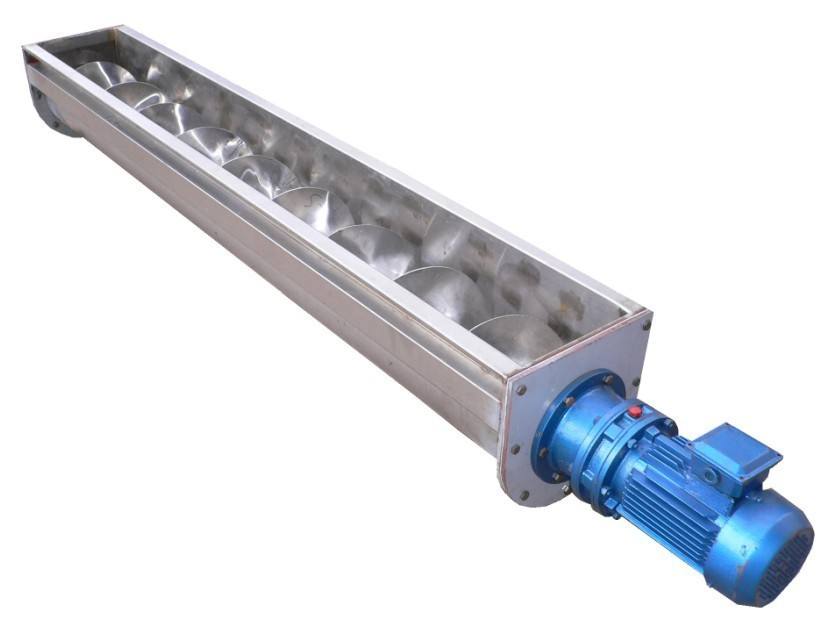
If you have any questions, please contact with us directly. Welcome you can visit our Factory.For inquiry,Please send mail directly to us.
Flour Machine Conveying Equipment
Flour Scraper Conveyor,Spiral Conveyor Equipment,Scraper Conveyor Equipment,Scraper Conveyor Machine
Shandong Hengyi kaifeng Machinery Co.,Ltd , https://www.xhykf.com