How to Enhance Robotic Welding Safety in Your Workplace
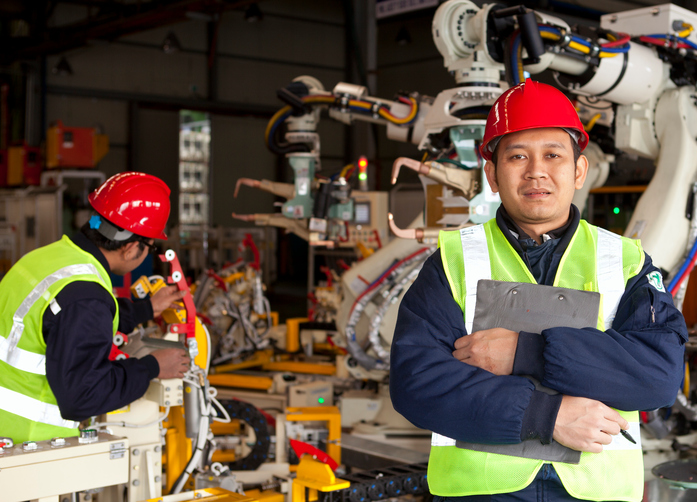
Robotic welding is a powerful and efficient process, but it also comes with significant risks. As more manufacturers adopt robotic welding systems, ensuring safety has become more critical than ever. Companies have a duty to protect their workers and maintain a secure environment that supports both employee well-being and operational efficiency.
Safety in robotic welding isn't just about installing barriers or guards. While physical safeguards are essential, they are only part of the equation. A truly safe robotic welding environment requires a comprehensive approach that includes training, risk assessment, and continuous improvement of safety protocols.
The Real Costs of Ignoring Robotic Welding Safety
It might seem expensive to invest in safety equipment, conduct regular training, and maintain your robotic systems. However, the cost of neglecting these responsibilities can be far greater. A single incident could lead to OSHA violations, costly fines, downtime, medical expenses, legal actions, and higher insurance premiums.
More importantly, workplace accidents can harm your company’s reputation and employee morale. Implementing strong safety measures not only protects your team but also strengthens your bottom line by reducing risks and improving productivity.
Taking Action for Robotic Welding Safety
The first step toward a safer robotic welding environment is understanding the existing safety standards. Organizations like OSHA, ANSI, RIA, and AWS have developed detailed guidelines to help manufacturers implement best practices. Familiarizing yourself with these standards is crucial for compliance and long-term success.
Training is another key component. Operators who work closely with welding robots must be fully trained and certified. With staff turnover common in manufacturing, it's easy to lose track of who has received proper training. Regular refresher courses can ensure that all personnel are up-to-date and aware of the latest safety procedures.
Conducting a thorough risk assessment is equally important. Even the most advanced robotic systems can fail, leading to serious hazards. By identifying potential risks—such as mechanical failures, software glitches, or human error—you can put preventive measures in place to minimize the impact of any incidents.
Companies that prioritize robotic welding safety often see improved performance and profitability. A safe working environment reduces accidents, increases efficiency, and fosters a culture of responsibility and care. It’s an investment that pays off in the long run.
Robot safety is not just a regulatory requirement—it’s a moral obligation. Protecting your employees from harm is essential, and doing so can also enhance your company’s reputation and financial stability. Take the necessary steps today to create a safer and more productive workplace.
nut packaging machine,cashew packaging machine,almond packing machine,peanut packaging machine
FOSHAN HIGH-TECH MACHINERY EQUIPMENT CO., LTD , https://www.packingweigher.com