How to Enhance Robotic Welding Safety in Your Manufacturing Process
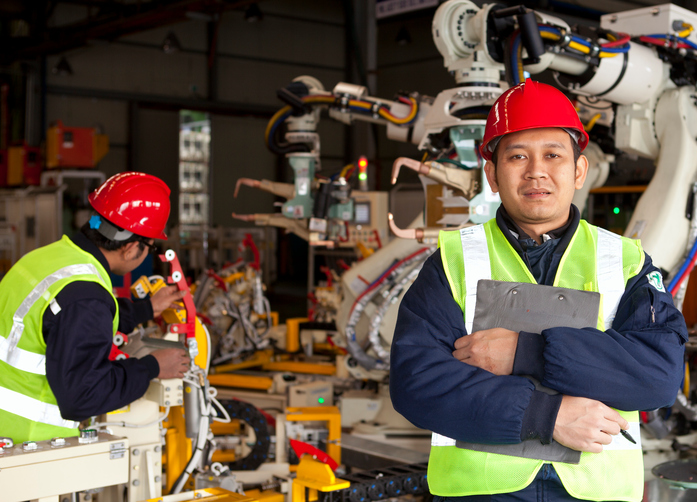
Robotic welding is a powerful and efficient process, but it also comes with significant risks. As more manufacturers adopt robotic systems, ensuring the safety of workers and equipment has become a top priority. Implementing and maintaining strict safety protocols isn't just about compliance—it's about protecting people and preserving productivity.
While physical barriers and protective measures are essential, they're only part of the equation. A truly safe robotic welding environment requires a comprehensive approach that includes training, risk assessment, and continuous improvement.
The Real Cost of Neglecting Safety
Investing in safety can feel like a burden, especially when budgets are tight. However, the cost of ignoring safety protocols can be far greater. Workplace accidents can lead to OSHA violations, costly fines, lost time, damaged equipment, legal expenses, and higher insurance premiums.
More importantly, a single incident could harm an employee or even result in a fatality. That’s why safety isn’t just a regulatory requirement—it’s a moral and financial responsibility for every manufacturer.
Taking Action for a Safer Workplace
The first step in promoting robotic welding safety is understanding the standards and resources available. Organizations like OSHA, ANSI, RIA, and AWS have developed detailed guidelines to help manufacturers create safe environments. Familiarizing yourself with these standards is key to staying compliant and reducing risk.
Training is another critical component. Operators must understand how to interact safely with welding robots, and this knowledge should be regularly reinforced. With staff turnover common in manufacturing, keeping track of who is trained and who isn’t can be challenging. Regular refresher courses ensure that all employees are up to date on the latest procedures.
Additionally, conducting regular risk assessments helps identify potential hazards before they become serious issues. Robots, like any machinery, can malfunction. By anticipating worst-case scenarios—such as mechanical failure or uncontrolled movement—manufacturers can implement safeguards that prevent injuries and downtime.
Ultimately, prioritizing robotic welding safety leads to a more efficient and profitable operation. A safer workplace reduces incidents, improves morale, and enhances overall productivity. It's a win-win for both employees and the business.
If you’re looking to improve your robotic welding setup and ensure long-term safety, consider partnering with experienced integrators like Genesis Systems Group. Their expertise in robotic welding integration can help you build a safer, more effective production line.
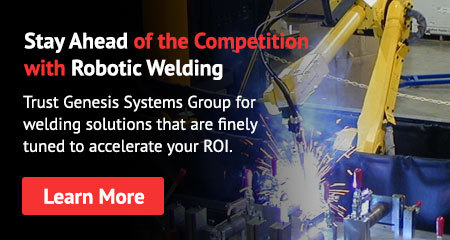
z bucket elevator,z bucket conveyor,z elevator conveyor,z type bucket conveyor
FOSHAN HIGH-TECH MACHINERY EQUIPMENT CO., LTD , https://www.packingweigher.com